摩尔定律预测,集成电路上的晶体管数目,在相同面积下,每隔18个月数量就会增加一倍,芯片性能也会持续提升,此定律在半导体产业发展将近60年之后,逐渐走向极限。(数据源:闳康科技;文章编修:科技新报)
各大厂也相继思索找寻新的解决方案,希望可以在无法缩小晶体管的情况下,持续提升芯片整体性能,并通过系统集成方式,来层层堆栈半导体电路,达到性能的跃进。而其技术关键就在于“封装”的“异质集成”来延续摩尔定律,而先进封装的最大优势────就是大幅缩短了不同裸晶间的金属连导线距离,因此传输速度大为提升,也减少了传输过程中的功率耗损。
目前各家芯片厂与封测厂皆发展自家先进封装技术,从技术及资本支出来看,以英特尔与台积电投入最为积极,两家合计投入的资本支出达整体产业55%,技术也最为领先。
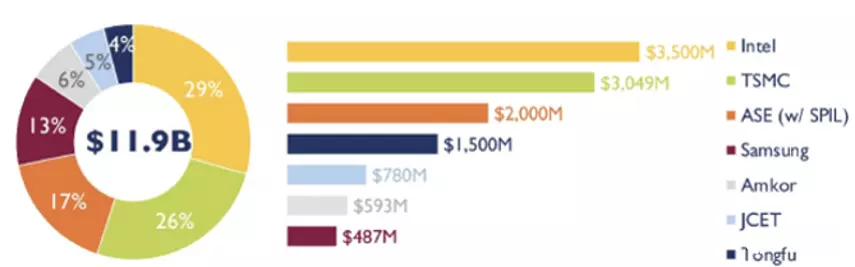
图一国际各厂商在先进封装的投资金额与占比“1”
AI芯片需求推动先进封装测试产业革新以台积电为例,先进封装技术可分为2D的InFO(扇出型封装)、2.5D的CoWoS(Chip on Wafer on Substrate)以及3D的SoIC。其中InFO技术最成熟也最便宜,约占先进封装产能的70-80%(每年8-10万片),并已大量运用在Apple的A系列及M系列芯片。随着AI芯片需求的急速增长,先进封装技术CoWoS的产能需求也同步攀升,带动了向来较少受到关注的半导体“测试”产业焕发新貌。闳康科技秉持与产业趋势共进的策略,深耕先进封装的失效分析,累积了丰富经验。以下将一一解密关键应用工具与技术。
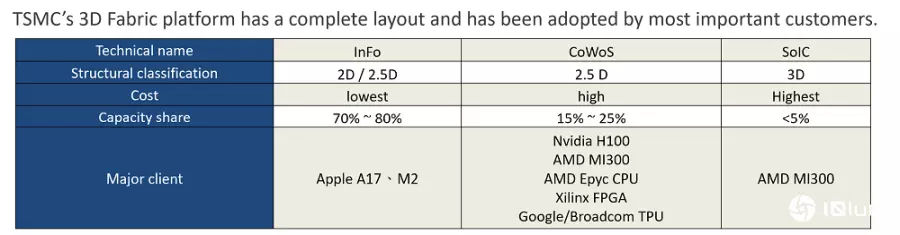
表一台积电的3D Fabric平台布局完善并获重要客户采用“2”
2D X-ray检测特性借由高能量撞击金属靶材激发出的x-ray具有穿透特性,借此成像以观察及判断先进封装内部是否存在空焊、HIP或Hop等现象,也可通过此工具快速的确认封装内是否有断线与严重烧融等缺陷。
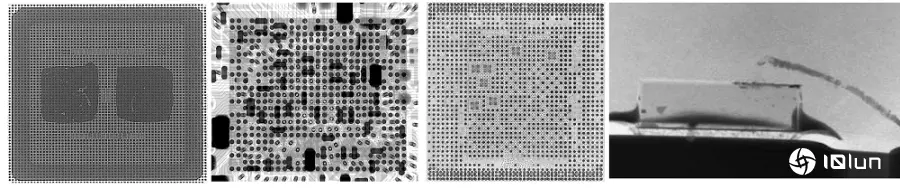
图二2D x-ray就如同封装健检,负责查看封装内部的结构与查找缺陷
SAT(CSAM)检测特性SAT又称为CSAM,借由超声波于不同密度材料的反射速率及回传能量的不同而形成形象,并依超声波的穿透率选用不同频率的探头借以侦测先进封装内部各界面层是否有脱层、空洞或是裂缝等异常现象。

图三SAT在封装健检中扮演查找封装内部缺陷的角色
3D X-RAY应用:非破坏性检测与高分辨率成像什么状况下需要使用3D X-RAY机台呢? 当失效样品仅有一个,无法直接进行破坏性分析时,我们建议可以针对异常区域执行超高解析的非破坏性3D X-RAY机台。闳康目前拥有ZEISS Xradia 520与620 Versa高分辨率三维X光显微镜 ( High Resolution 3D X-ray Microscope) 设备。
3D x-ray原理就是以高能电子重击金属靶材 (W) 后,产生短波长、高能量且具有强穿透性的X-ray射线,穿透待测物产生绕射波,侦测器接收后,经由闪烁体转换成可见形象,并利用样品在载台上360゚旋转的方式得到空间中各种不同方位的2D X-ray断层形象,并配合计算机演算将这些形象组合成待测物的3D X-ray断层形象,这也是计算机断层成像的原理。3D X-ray的分辨率取决于像素大小,越小分辨率越好。目前机台在空间分辨率的极限为0.5 𝜇m,且机台内有12种标准Filter (滤镜) 可以自动调整,侦测器有5种镜头 (0.4X、4X、20X及40X) 可使用。
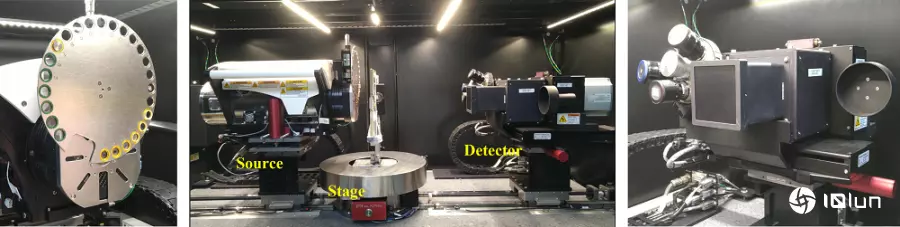
图四3D X-ray的硬件架构
先进封装结构相对复杂,失效的样品若可以通过电性分析缩小异常范围,3D X-Ray即可以在较佳的扫描分辨率找出明显的缺陷,以下主要是针对CoWoS样品扫描之范例,图五 (a) 可以明显看出TSV异常位移,图五(b) 介质层 (Interposer) 有脱层现象,图五 (c) u-bump接合处有明显异常。
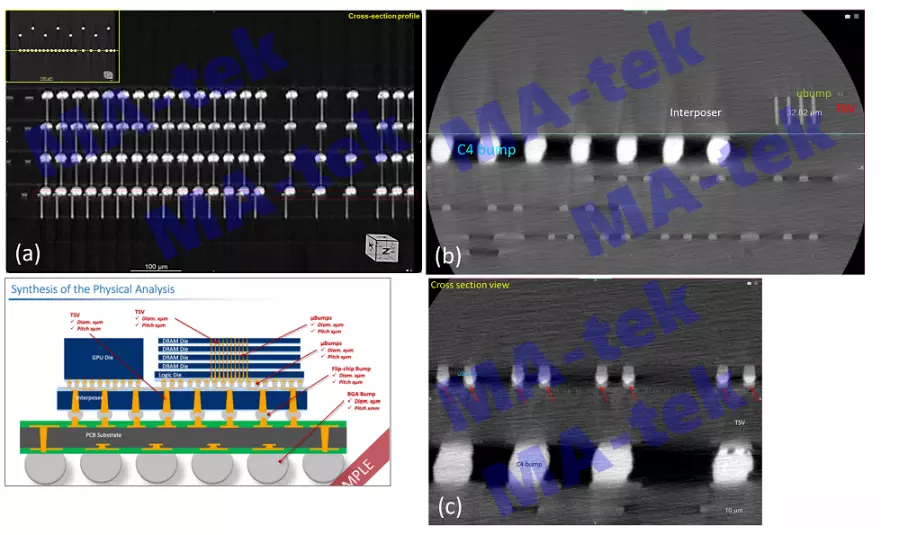
图五CoWoS封装结构示意图“3”与常见的缺陷类型
TDR技术:精准定位先进封装中的断路与异常时域反射仪(Time Domain Reflectometry,TDR)是一种常见的网络分析技术,主要用于测量信号在传输线或介质中的反射和衰减情况。在先进制程中,TDR技术在故障分析方面发挥重要作用,特别是在先进封装故障排除中,能够快速判断异常发生在芯片还是封装端,广泛应用于半导体制造、测试以及电子设备维修与故障排除。
TDR技术通过发射短脉冲信号,沿着被测线路(如封装或芯片内的连接线路)传输,并测量反射信号的时间和强度,以精确检测断路。当传输线完整时,TDR波形会呈现典型反射信号;若线路出现断路,则反射信号会异常,如强度变弱或消失,或时间延迟不符预期。通过对比好品、坏品和空板的结果,TDR可精确确定断路位置,区分异常发生在封装中的芯片或封装本身,并定位特定结构问题,如u-bump、TSV或C4 bump等常见封装结构或界面异常。
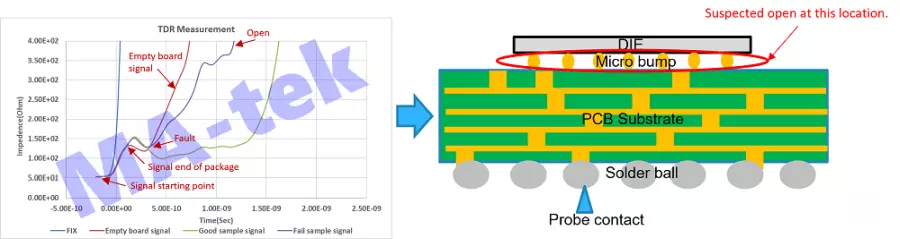
图六比较好品、坏品与空板的TDR的波形,判断可能的断点是在u-bump
LIT:高分辨率红外热成像技术LIT又称为Thermal Emission Microscopy,能够有效及快速的对2.5D与3D的先进封装失效热点进行定位。而有缺陷的半导体设备通常会表现出局部功耗的变化,导致局部温度升高,LIT能够通过红外热成像技术来检测物体表面的温度分布,识别出可能存在的故障问题,并利用锁定 (lock-in) 红外线热成像来提高定位的精准度,以提供后续非破坏性 (3D X-ray) 与破坏性切片的封装缺陷观察结果。
LIT技术利用高灵敏度的InSb(锑化铟)侦测器,在通电状态下捕捉待测物缺陷产生的热辐射,精准定位失效点,甚至能估算热源的深度。其主要特点包括:
- 高分辨率红外热成像:高分辨率的红外热成像技术,能够捕获物体表面微小温度变化的细节。
- 故障检测和分析:通过检测物体表面的异常温度,可以快速识别出潜在问题,例如电子组件过热或设备热失效等。
- 故障机制检测:可检测于产品短路、ESD缺陷、氧化物破损、设备闩锁、有缺陷的晶体管与二极管。
总的来说,Thermal Emission Microscopy是一项强大且高效的热形象分析技术,能快速精准地定位故障热点,有助于提升故障分析的效率与准确性。
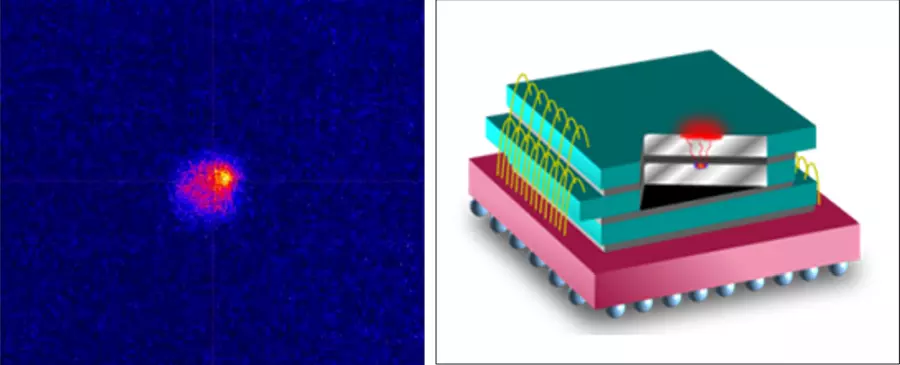
图七Thermal Emission Microscopy能在不开盖的情况下精准侦测失效点的平面位置,并在纵向上识别出故障点位于哪一层芯片或基板。
P-FIB技术在先进封装失效分析中的应用在封装与芯片的失效分析上,最初以研磨切片为主要分析方案,随着封装种类进步与多样,芯片内的I/O密度也快速地提高 “4”,其中提升芯片互联的接点密度,是2.5D/3D立体封装的发展趋势 “5”,当接点间隙缩小至10微米以下时,手工研磨将不足以准确的制备定点样品切片,而P-FIB在先进封装的失效分析上逐渐成为主要运用手法。
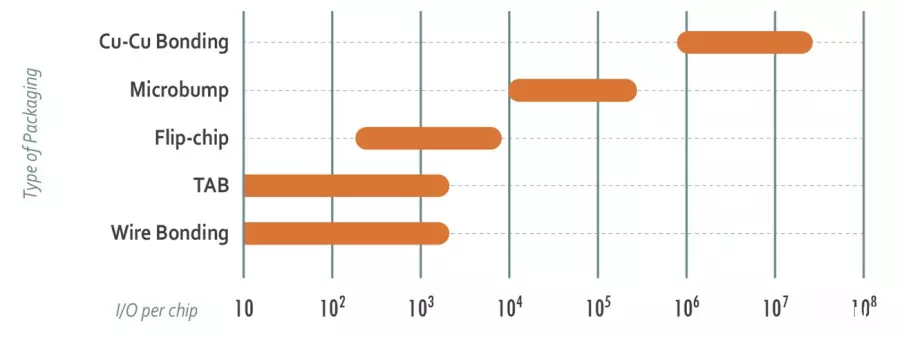
图八各种封装技术在1x1cm^2的芯片内能达到的接点数量“4”
P-FIB的应用除了结构的基本观察外,更可使用在热点或非破坏分析之后的检测验证上,比如以Thermal Emission Microscopy、OM、3D X-ray或SAT观察到异常之后,便可利用P-FIB在异常处做截面上的确认。“6”
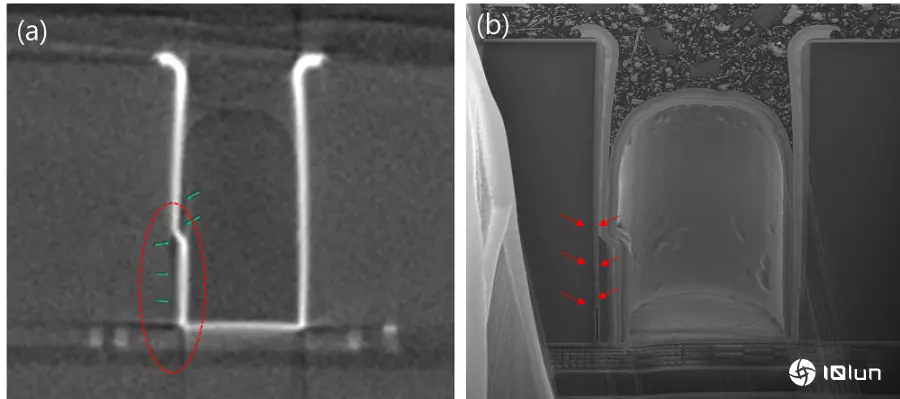
图九针对(a) 3D X-ray观察到TSV变形位置执行(b) P-FIB粗挖+ FIB细修
DB P-FIB切割面积可达500um宽与500um深,可用于观察先进封装的结构,比如C4 bump/interposer/u-bump/TSV/fine pitch RDL,在削切截面的过程中,同时以SEM方式观察削切的情形,可即时判断缺陷的变化。
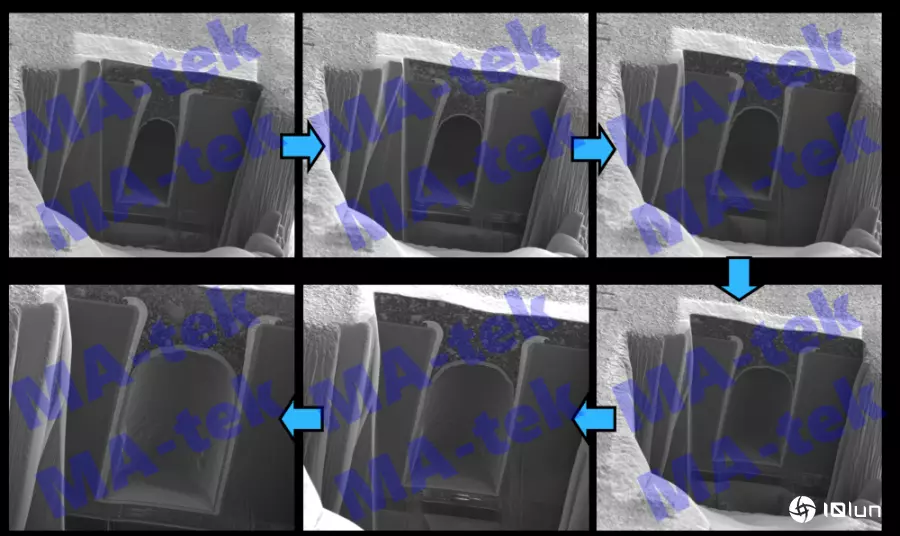
图十FIB切削TSV的连续过程
样品制备:故障分析的关键环节样品制备 (sample preparation) 在故障分析中扮演着至关重要的角色,是决定分析成功率的最大因素,尤其在先进封装失效分析流程中更加关键。通过制备的过程,包括手工/自动研磨、化学蚀刻等步骤,每一个细节都考验着操作人员的经验和细心程度。闳康团队在高端先进封装领域拥有丰富的经验,借助成熟的样品制备能力,我们成功地发现了封装内部各种缺陷,为后续的故障诊断提供了可靠的依据。
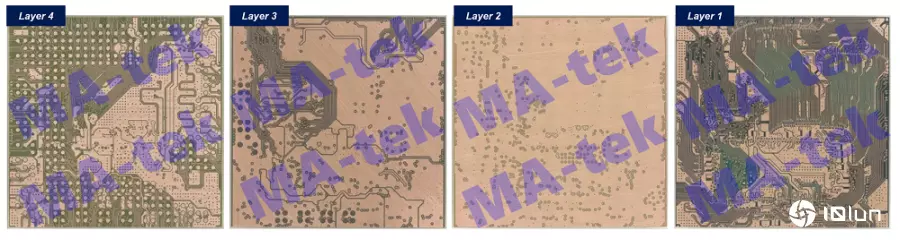
图十一P-Lapping手工研磨技术(BGA)
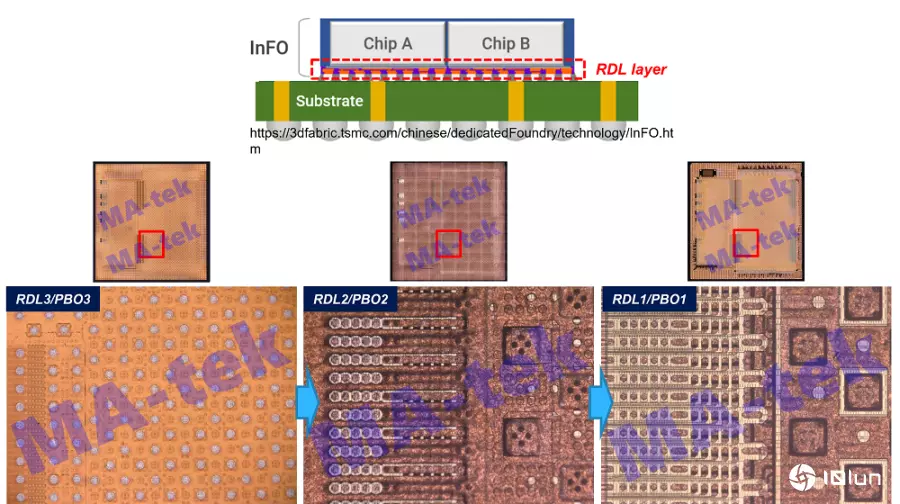
图十二P-Lapping手工研磨技术(InFO_oS) “7”
SEM样品制备:影响观察与分析结果的关键样品制备前处理及搭配电子显微镜观察是对先进封装失效分析常使用到的方式,处理方式将会直接影响到最终的观察及分析结果,以下枚举几个SEM样品制备的重要性质。
- 去除污染和杂质: SEM能够以极高的分辨率观察样品表面。在进行观察之前,样品必须经过适当的清洁,去除任何可能影响结果的杂质或污染机台的液体、挥发物、粉尘。
- 提高导电性:SEM样品要求良好的导电性,以避免在分析过程中静电放电,这可能损害样品并对拍摄形象产生干扰,因此部分非导电物质在进行SEM拍摄之前皆会进行表面镀金或镀碳,以提高形象品质。
- 适当的固定和切割:因SEM载台大小有限,样品需要裁切以便能够被固定在载台上,目前闳康科技所使用的机型可以放置六英寸芯片以内大小的样品,高度限制为5厘米,目前常使用的材料都能够进行裁切,例如芯片、载板、陶瓷材料、金属、玻璃、高分子材料等。
- 获取特定区域的资讯:如果有特定的垂直结构需要观察,这时候就需要做定点样品制备(切片),通过研磨以及抛光,甚至是离子束切片,我们可以精准的切到约1um大小的结构并进行SEM拍摄,更小的目标也可以借由FIB和TEM来进行样品制备与拍摄。
- 提高分辨率和对比度:正确的样品制备可以帮助提高SEM的分辨率和对比度,我们借由一些表面处理来获得更多样品消息,常使用的方式为化学药品的表面微蚀、离子束的表面抛光或深切、Plasma清洁等等。
通过上述介绍的相关手法,我们在进行研磨之前,首先会将样品镶埋于环氧树脂中,这样可以有效保护样品结构,防止在研磨过程中对样品层次造成损坏。选择合适的砂纸号数和材料也非常重要,应避免使用颗粒过大的砂纸,以免对样品表面造成不必要的损伤。研磨后,我们会使用抛光液和绒布进行细致的抛光处理,确保表面光滑且平整,为后续SEM拍摄和异常观察提供理想的截面。
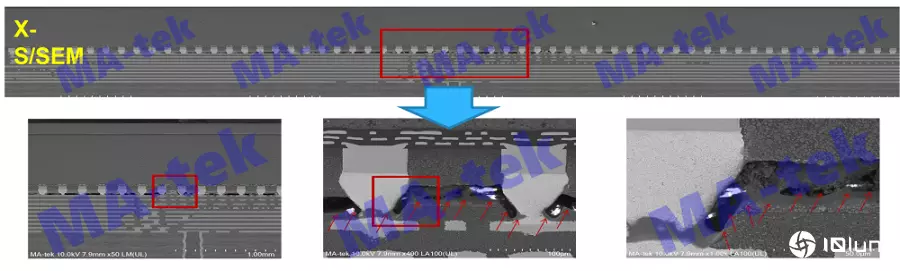
图十三BGA封装经过研磨后再以SEM针对异常处放大观察
搭着AI的浪潮,高运算芯片与先进封装的产值在半导体产业愈趋增长,这些设计与结构上的复杂度使得故障分析面临空前的挑战,而在先进封装的失效解析中,只要采用本文介绍中的各个技术与方法,无论是进行缺陷定位还是提高观察精确度,都能取得显著的效果。
参考数据:“1” Yole“2” Fugle
“3” EETimes
“4” King-Ning Tu, Chih Chen, Hung-Ming Chen, Electronic Packaging Science and Engineering, Wiley, 2021
“5” https://www.matek.com/zh-TW/Tech_Article/detail/specialist-column/all/202207-IAR (3D IC封装:超高密度铜-铜异质接合)
“6” https://www.matek.com/zh-TW/services/index/P-FIB
“7” https://3dfabric.tsmc.com/chinese/dedicatedFoundry/technology/InFO.htm
(数据源:闳康科技;首图来源:Shutterstock)