应对地缘政治、全球化生产短炼化、远程协作日益盛行等全球变局,台达推出辅以AI技术与模型的数字双生(Digital Twin)解决方案,以协助电子组装业完美解决少量多样、产品生命周期缩短、缺工以及高品质生产等挑战。
在董事长暨首席执行官郑平的带领下,台达自2015年推动DSM台达智能制造(Delta Smart Manufacturing)计划,从设备自动化全面走向智能化。有了这样的数字转型与智能工厂转型基础,台达开发出满足电子组装与半导体产业“分散制造、集中管理”需求的解决方案。
台达智能制造软件新业务发展部处长陈鸿辉表示,为了将原有产能、良率,甚至管理文化完善地复制到全球不同的生产制造场景,台达推出专为分布式制造量身打造的Line Manager,让客户可借由该软件连接IT与OT层,将生产全面数字化并存储为数据库,成为本地化生产系统的大脑,管理人员可以远程集中调控当地产线。
通过台达DIATwin数字双生解决方案,便能在云计算上打造一个拥有现场实体设备及产线所有资讯的虚拟分身设备,客户可以预先在云计算虚拟产线上进行调试,之后再将全局配方或制程参数下载到当地产线机台上直接生产。不仅如此,DIATwin还可搭配AI,打造不断调适优化为更精准数据模型的封闭循环生态系统。
台达智能制造系统集成新业务发展部处长陈霈宇指出,台达DIATwin除了能协助企业客户兼顾品质、成本、交期及服务(Quality, Cost, Delivery, Services,QCDS)以及快速弹性的新产品导入(New Product Introduction,NPI)之外,尤其注重单一机台设备分身的模拟能力,因而能为客户提供快速的可制造性设计(Design for manufacturing)模拟与完整的企业移动管理(EnterpriseMobile Management)评估。
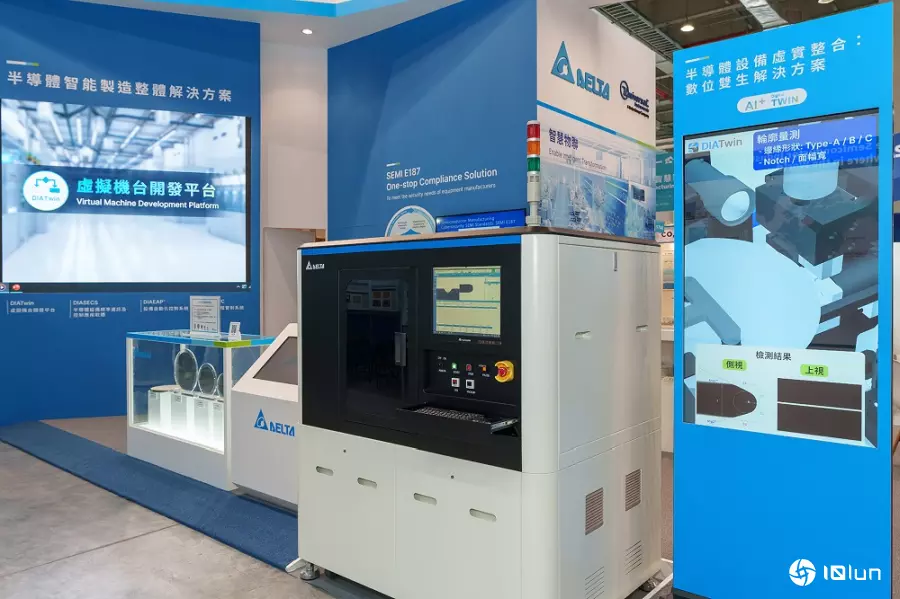
2024年国际半导体展SEMICON Taiwan上,台达展示DIATwin虚拟机台开发平台,示范如何将数字双生物科技术应用在前端制程的芯片轮廓仪。
数字双生成为缩短开发周期,满足分散制造需求的最佳解决方案数字双生物科技术能够同步消弭虚实差异、降低研发制造风险并缩短产品开发周期,已然成为半导体及电子组装产业应对本地化制造风潮的最佳解决方案之一。
当地缘政治的冲击下,当前制造业面临制程需求复杂多变、产能评估困难、交期难以掌握、开发/测试成本高、参数调机耗时,以及人员经验难以复制等痛点,通过数字双生物科技术的导入,便能为企业带来显著的效益与转机,不仅能加速产线与设备的布局规划、提供高拟真的制程模拟,进而降低试错成本,还能发挥知识传承与人才培训的效益。
陈鸿辉强调指出,企业想要导入数字双生,先决条件就是要有数字化转型作为升级的基础。更关键的是,必须兼顾精准的数据采集与高拟真度的模拟,如此数字双生平台才能为实体机台设备提供优化的句柄、产线配方与制程参数。
陈霈宇补充指出,对于分布式生产,必须同时具备集成设备设计制造、自动控制、软件开发以及AI应用等四大面向的能力,才能确保数字双生可以快速有效地在场景落地导入并产生效益。当前许多制造业客户在导入数字双生时常见的最大缺口莫过于机台虚拟分身,而构建机台分身正是台达的强项所在。
台达推出的数字双生解决方案,同时结合DIATwin虚拟机台开发平台以及RTM虚实集成设备(Reconfigurable Transformer Machine),适用于电子组装、半导体、车用电子、建筑、制鞋以及五金加工取放等产业。
通过高拟真的3D制程模拟及参数优化模块,DIATwin能够极具成本与时间效益地预先进行单机/整线模拟,并在虚拟机台中通过HiL虚拟调机(Hardware in Loop)功能持续调试出优化的制程参数,大幅提升总公司与当地产线之间以及用户与设备制造商之间的沟通效益,加速新产品导入与上市时间。
DIATwin平台能够高拟真模拟但凡干涉、流体力学、动力学等物理现象,并可集成PLC/PC-based控制器、工业机器人、服务器驱动器、传感器、视觉相机与取放夹爪等台达系列产品。换言之,通过高拟真物理引擎以及组件/整机布局数据库,能够弹性满足不同生产需求,有效提升机台与产线的生产效率。
至于高度模块化的RTM,能集成各组件的控制核心,赋予机台自动校正机差的能力。除了自动校正与标准模块等功能外,RTM与DIATwin的搭配,更能发挥虚实集成的最大效益,更是应对当前少量多样生产需求的最佳解决方案。
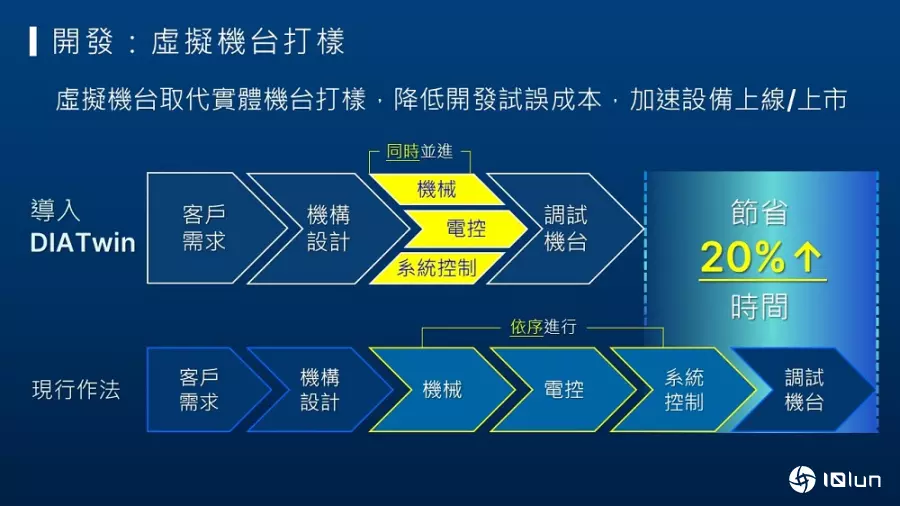
DIATwin虚拟机台开发平台,通过同步进行的机械、电控与系统控制模拟,成功节省20%设备上市时间。
打破OT与IT沟通障碍,台达DIACFX打造智能工厂机联网想要成功导入数字双生物科技术,除了前述的数字化基础、良好数据采集与高拟真模拟之外,为了让OT与IT沟通无碍,制造业还必须确保自家设备支持CFX(Connected Factory Exchange)通信标准。该标准是IPC协会专为电子组装产业打造的国际通信标准,系工厂产线设备之间创建M2M通信与机联网的通信协议,也是数字双生的运行基础。
对此,台达推出电子组装设备专属的通信协议和通用数据模型解决方案DIACFX,协助客户快速将该标准导入设备,彻底打破定制化数据通信成本高昂、OT与IT沟通不良以及上位系统资讯集成不佳等障碍。
该方案并且针对PC设备与PLC设备等不同程序开发人员分别提供DIACFX SDK软件开发组件以及DIACFX Box通信盒。前者不需开发程序,只需将设备数据传入DIACFX SDK中,该组件会自动处理好一切,包括通信时的数据模型格式。后者支持多家PLC控制器,开发人员只需使用原本熟悉的PLC开发,再将数据写道PLC点位,通过简易设置,DIACFX Box便可即插即用,让产线设备联网。
陈鸿辉表示,传统工业物联网多半采用Rule-based机制进行各种数据联网应用,但数字双生则采用更直觉、敏捷的Model-based互联机制,通过CFX标准,即时发送描述各种设备或产品状况,例如稼功率及生产履历等个别数据模型。
AI增值助力数字双生,实现更高拟真度的虚拟模拟数字双生最引人瞩目的特点莫过于在虚拟世界里打造出和实体设备几乎一模一样的高拟真虚拟分身。但以目前的技术而言,即使再高的拟真度仍然会有落差。针对这个问题,陈鸿辉表示,此时AI即派上用场来弥补这个落差。
台达旗下子公司达慧互联便为客户提供端到端的专家顾问服务,由机械与制程领域的专家顾问,采集整理客户专属的OT数据,设计出各种可立即落地的AI模型,包括提供预测性维护的PdM AI、通过视觉识别技术确保品质的Quality AI、掌握设备节能减碳状况与效益的Green AI,以及降低职场安全风险的Safety AI等模型。通过这些模型,不但可以弥补数字分身的落差,还可加快客户导入数字分身的脚步。
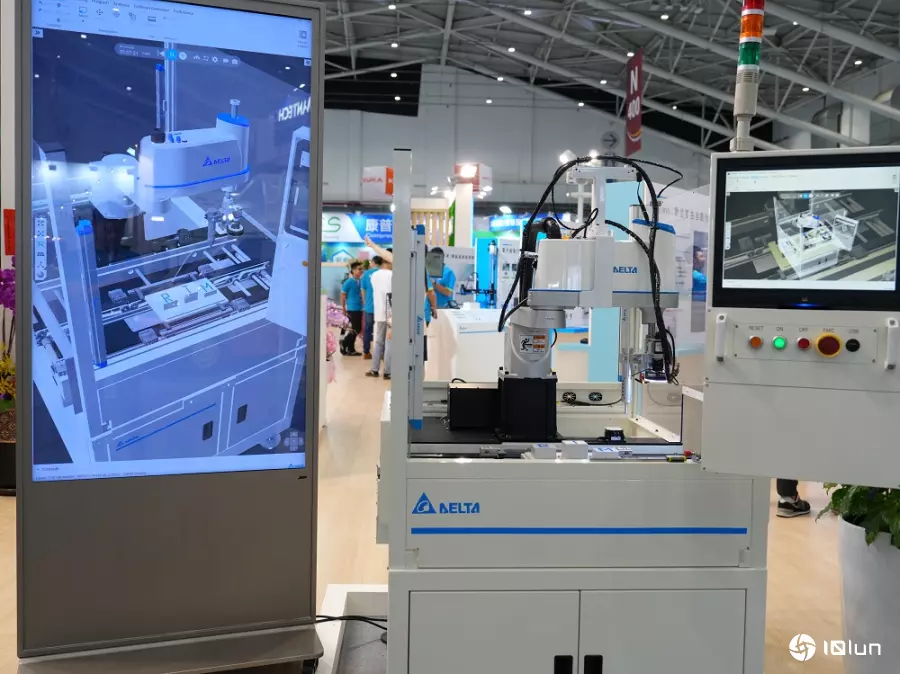
台达DIATwin解决方案,集成AI运算与数字虚拟技术,加速机台开发上市。
陈霈宇表示,对于许多制造业厂商而言,数字双生的导入就像数字转型一样需要长时间的投入。台达提供相对精炼的解决方案,再搭配上述AI模型顾问服务的导入,相信能协助90%以上的客户加快导入的进程。
台达有许多DIATwin搭配AI助力厂商提升生产效率的案例,该公司曾助力电子组装大厂创建高拟真数字喷胶机台,以及包括胶体颜色、喷涂形状/高度/压力、I/O信号延迟及涂胶分布等精准的数据驱动模型,成功缩减80%以上的调机时间。此外,台达曾协助厂商创建涵盖加速度、夹持力、信号延迟及真空压力等精准的数据驱动模型,成功通过AI升级取放夹持制程。
落实零人力、零停机、零缺陷,将精力放在创造而非制造上台达DIATwin数字双生解决方案能分别在售前、开发与调机等不同阶段带给客户显著的效益。整体而言,该方案能节省20%的设备开发时间,包括新产品设计、构建到调试的进程。台达希望未来能进一步达到50%以上。
在售前阶段,可通过Web 3D互动界面快速创建机型/方案比较、布局评估与干涉检测,有助于完成机台设计共识与下单决策。在开发阶段,可进行虚拟机台打样,通过高精度的模拟,展现各种虚实集成应用的效益,不仅有助于提升产线稼功率与产能,更是OEM或合约制造商在设备打造之前,便能提前向品牌客户展示虚拟设备面貌的提案利器,对于加速设备上线/上市极具帮助。
在调机阶段,设备上线后也能在虚拟机上通过示波器验证进行脱机调参,不仅有效缩短调试时间,打造定制专属的虚拟机台,并且在虚实集成下无缝地将优化参数套用在实体机台上,实现机台增值与设备产能优化。
陈霈宇表示,台达推出数字双生解决方案的宗旨,在于提供产业客户符合开放标准、最低成本、最佳模拟效果,避免被特定设备、协议或厂商绑定的最佳分布式制造解决方案。
预期未来,陈鸿辉表示,凭借数字双生创建的虚实集成系统与在智能制造累积多年的丰富经验,台达期望未来能打造自主化智能工厂,实现零人力、零停机、零缺陷“三零”制造愿景,让“将人的精力与脑力放在创造上而非制造上”的愿景获得完美落实。
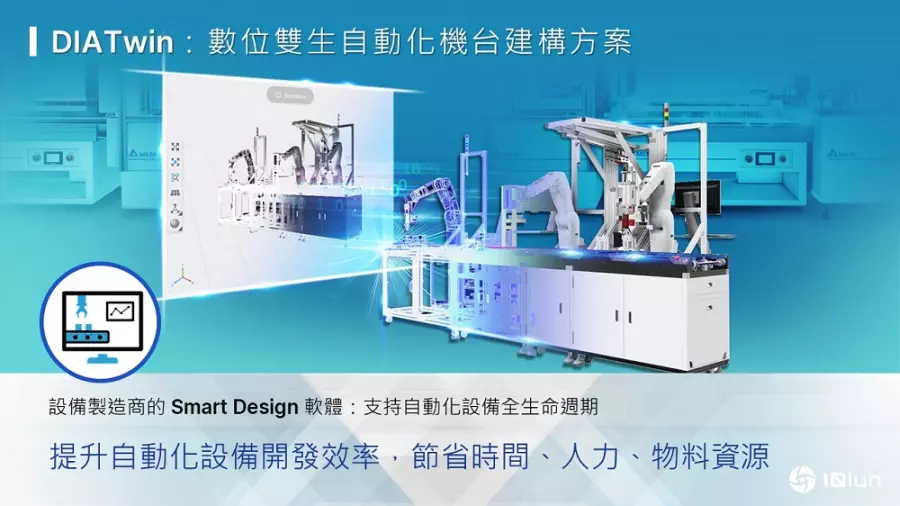
(图片来源:台达电子)